CNC Precision Machining: What Is It and How Does It Work?
High-end metal engine parts, tools, and equipment require a high degree of precision to manufacture. After all, they can’t be cast in a furnace or cut by hand since they are produced by machines built for precision milling and cutting.
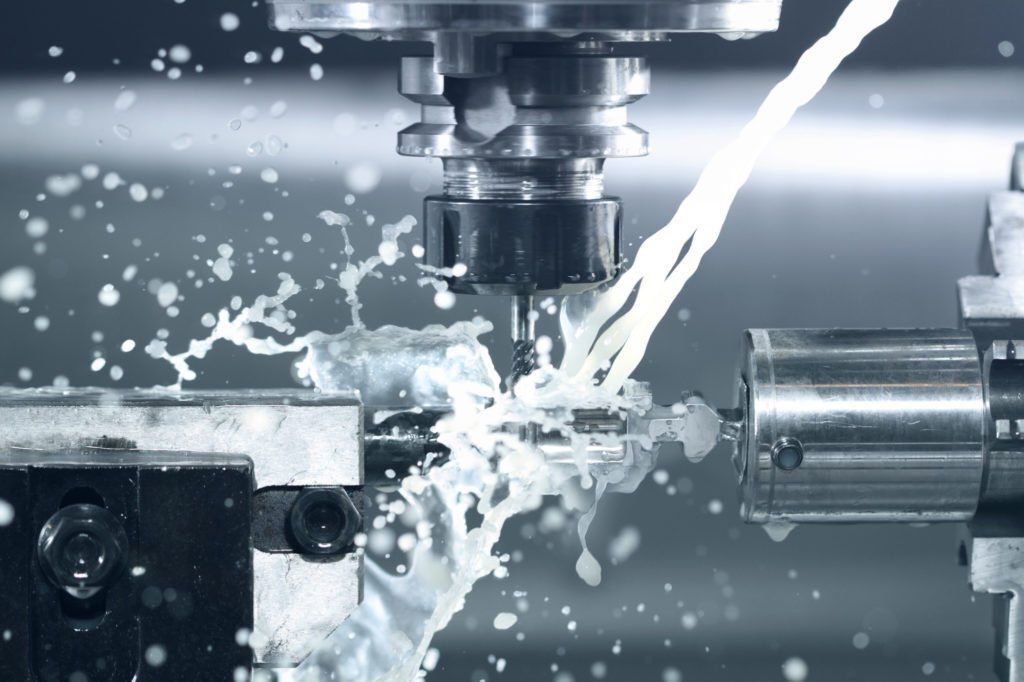
Major industries like automobiles and aerospace manufacturing have extremely high demands for the quality and accuracy of their custom-designed parts and equipment. If you’ve ever wondered where all those parts came from, it’s time to understand how precise CNC machining parts are made.
What Is CNC Precision Machining?
The basic concept behind CNC precision machining is that it’s a manufacturing process that uses software to design products to precise specifications and then shapes the raw material into that “mold” to produce a finished product. You can think of the precision machining process like this:
- Designs, which are detailed blueprints or representations of what the object will look like in three dimensions, are typically made in software enabled for Computer-Aided Design (CAD).
- Then Computer-Aided Manufacturing (CAM) software converts those designs into instructions for the CNC machine.
- From there, Computer Numerical Control (CNC) equipment cuts, mills, and processes the material into the desired final product.
This general overview is a gross oversimplification of what the technology can accomplish, and much of it is actually automated as the precision machinist only has to input the data and let the cutting tools do the work.
What the CNC Machining Process Looks Like
To be more specific, we can look at what gets accomplished at each stage of the CNC machining process. It begins with a choice of materials, which can include anything from metals like copper, steel, and aluminum to plastics like ABS and PMMA. The exact raw material depends on the strength, cost, and properties necessary for the final product.
The machinist programs use CAD to generate blueprints, which the CAM software uses to create digital code that controls the actual tooling. This machine code involves geometric code (G-Code) that tells the machine how to carve out the design physically. It’s complemented by M-Code, a miscellaneous machine code that provides auxiliary functions.
An important concept to grasp in CNC precision machining is tolerance. While CAD blueprints and machine drills can’t be perfectly precise, the machinist still defines a maximum amount of acceptable deviation in the final product. If this tolerance is too high, then the final product may have its quality compromised. If it’s too low, then the production cost to manufacture will go up exponentially.
Once the machine starts processing the materials, it goes through various CNC processes that we’ll discuss later, from CNC milling to turning and drilling. Finally, the product is given a finish for strength or aesthetics, such as electroplating or anodizing.
What Are Some Types of Precision CNC Machining Equipment?
Given the many processes involved in CNC machining, it should be no surprise that many different types of equipment exist for this stage of manufacturing.
- Milling Machines use rotary cutters to remove excess material from the product. Examples include chamfer mills and helical mills among others.
- Turning rotates the product itself and allows a stationary cutting tool to come into contact with it. Examples here are straight turning, taper turning, and threads.
- Drilling is exactly what it sounds like. Much like a power drill in a toolshed, this rotating drill bit is used to create holes in the raw material. There are spotting drills, peck drills, chucking reamers, and other versions.
- Spark machining, also called Electrical Discharge Machining, uses electrical discharges to process the material. A dielectric fluid separates the product and the machine, and a voltage is applied to begin the procedure.
CNC precision machining factories need to work with various types of machine tools for the same project.
The Impact of CNC Precision Machining on Modern Manufacturing
Why do so many industrial applications exist for CNC precision machining? Companies in many markets are recognizing the advantages of this form of manufacturing.
The Advantages
When compared to alternate methods like injection molding, CNC machining can achieve high standards of precision without the high upfront cost involved with creating a mold.
It’s also much faster. Compared to injection molding, which can take months, precise machining only needs a few weeks at most. This benefit is why CNC is popular for creating prototypes, as it can accelerate product research and development.
Applications in Various Industries
Precision CNC milling makes sense in a lot of contexts. The advantages of CNC lend it well to various use cases throughout multiple manufacturing industries.
- Aerospace Industry: Precise tools and parts like airfolds and gear ports are necessary to build safe planes and space shuttles. Any compromise on precision can result in severe safety hazards in the final product.
- Automotive Industry: The shipping industry uses CNC-machined parts to produce transport trucks and vessels. And consumer car manufacturers need to build prototypes to exact specifications for new releases.
- Defense Industry: Militaries of the world use CNC to build firearms, ammunition, transportation components, communication infrastructure, and various other supplies.
- Medical Industry: CNC precision machining technology is used to produce equipment for providing healthcare, which can include MRI machines, implants, and research equipment.
These are only a few of the many examples out there of how CNC machining is empowering manufacturing lines around the globe.
Work with a Tier-One CNC Precision Manufacturing Company to Achieve True Quality
Are you looking for machining services empowered by the most cutting-edge technologies available? Partner with GN Corporations to access the right tools and processes for your next project.
Whether you need welding, brazing, hard facing, coating, inspections, or even a complete assembly, we have everything you need to achieve your outcomes, on time and on budget.
Get in touch with us today to learn more about our
CNC precision machining services.