What is Welding? The Most Common Types of Welding Processes
Welding is an essential part of manufacturing countless products, ranging from automotive to defense. Manufacturers that require welding to complete their production process may handle it in-house, but many manufacturers choose to bring in a specialty supplier of welding services.
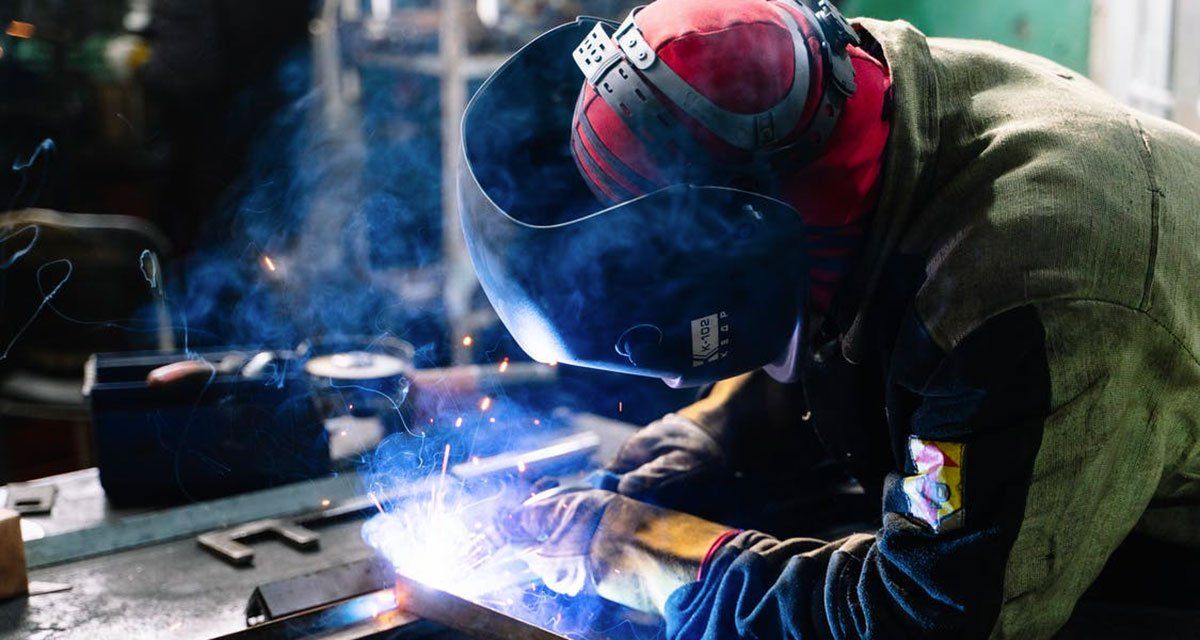
Many different types of welds are useful in different applications and industries. Therefore, it’s essential to understand the difference between each type of welding process and why a manufacturer may choose one type over another.
Today, we’ll dive into the world of welding by starting with the welding definition and then exploring some of the common welding processes that many manufacturers require. Read on to learn the facts about different types of welding, and some of the most common applications.
What is Welding? Welding Definition
How does welding work? Generally speaking, welding is a specific fabrication process in which two or more parts are fused together. Fusing these parts may include heat, pressure, or joining the parts as the metal cools.
Welding is known for its usage with metals, but welding is also used to join thermoplastics and wood. The completed joint is often called a weldment. The two or more parts that are being fused together are called the parent material, while the material added to form the joint is called filler material or consumable.
Welding and fabrication are used to join many parent materials, but some materials simply cannot be joined together. Materials that cannot be joined are called ‘unweldable,’ since no known welding process will adequately complete the task.
The Different Types of Welding Processes
The welding process chosen to complete a task depends on the parent material's type and the specifications for the result. Different types of welding are put to use throughout manufacturing to accomplish a wide range of goals.
Let’s discuss some of the common types of welding found throughout the manufacturing world.
MIG: Gas Metal Arc Welding GMAW
When most people think of welding, they’re thinking of MIG welding. Arc welding processes are commonly used in both manufacturing and repair in the auto industry, and are known to produce clean welds. MIG welding can also be found in building construction, and is usually considered a form of welding that is easier to learn for beginner welders.
MIG welding is also known as gas metal arc welding (GMAW) and can use bare wire or a flux core to complete the task. Bare wire MIG welding is often used to join thin pieces of metal together, while a flux core welding is used for heavier duty tasks.
TIG: Gas Tungsten Arc Welding GTAW
TIG welding is similar to MIG welding but uses a tungsten electrode. Tungsten is among the most rigid materials; it won’t melt or burn off. As such, TIG welding uses a process called fusion and may not require a filler metal. TIG welding uses an external gas supply that can be either argon or helium.
TIG welding produces strong weldments and can be used for many common parent materials, including:
- Carbon Steel
- Stainless steel
- Aluminum and its alloys
- Chromoly
- Nickel alloys
- Magnesium
- Copper and its alloys
- Brass
- Bronze
- Gold
TIG welding is used in many aerospace applications as well as in the
automotive industry to produce strong weldments for many of their essential tasks.
Stick: Shielded Metal Arc Welding SMAW
Stick welding is a type of arc welding that uses a stick electrode welding rod. This welding process requires a consumable and a protected electrode or stick. The stick softens and bonds the parent materials with an electric arc. As the stick melts, the protective cover also melts, which shields the welding area from gasses in the air.
Surfacing: Hard Facing or Wear Facing
Surface welding is different from the above methods as it is not used to combine two or more pieces. Instead, surfacing applies a hard, wear-resistant layer to the chosen material. Surfacing is commonly known as hard facing and may also be called wear facing.
Hard facing is commonly used to extend the life of tools, machines, or construction equipment. Surface welding can add a protective layer to many different components, such as gears, shafts, and cutting edges.
What Major Industries Use Welding?
You can find welding manufacturing put to use in many different industries, including:
- Automotive Manufacturing Industry
- Aeronautic
- Railroads and Trains
- Aerospace Manufacturing Industry
- Defense
- Construction and Infrastructure
- Maintenance
Each industry has unique needs and may use different welding processes.
Partner with GN - Your Provider of Precision Welding Services
Welding requires specialized equipment and training. Many manufacturers would instead use a welding service provider rather than expend the capital in operating their own welding services.
GN Corp has invested in the latest welding technology and equipment to provide precision welding services to our customers.
Our tier 1 fabrication services have made us a reliable partner in our customer’s success for decades.
Contact us today to discover how our precision welding services can help your company.