What Is Waterjet Cutting and Drilling?
When you think of industrial-strength cutting and drilling, you probably don’t imagine water being the main means of slicing through the material.
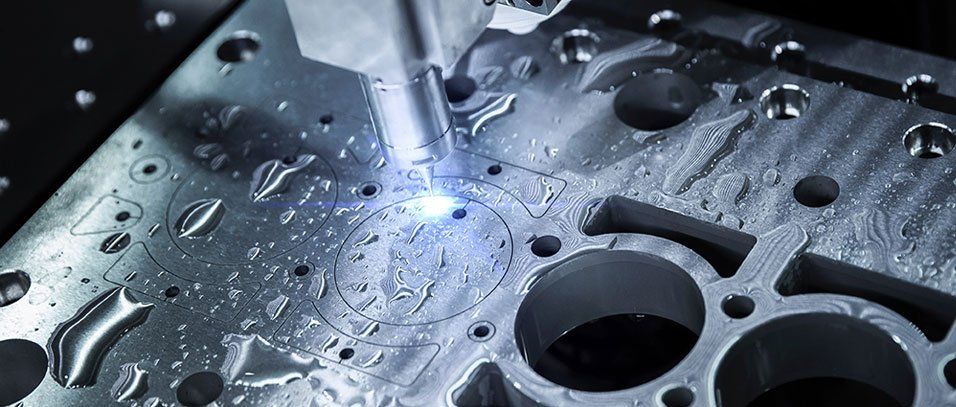
However, pressurized water is actually an incredibly strong cutting instrument. Industrial water drill machines use pressurized water in combination with an optional abrasive substance to cut through a wide array of hard and soft materials, from metal to wood to virtually anything.
The
waterjet CNC cutting can be found in a variety of industries from mining to aerospace and are common in the production of machine parts. Even artists sometimes use it to cut intricate shapes into glass or stone. A pure waterjet system uses only water for the job, while an abrasive water jet includes abrasive materials.
Read on to learn more about waterjet cutting and drilling, as well as how it's used in the manufacturing process.
How a Jet of Water Can Cut So Fluently
Waterjets work by forcing high-pressure water through a small hole known as a jewel. Much like covering up part of a garden hose with your thumb, the result is a strong beam of water that can cut through most materials.
Most jets pressurize the water between 20,000 and 93,000 PSI and use a jewel 0.18 to 0.4 mm in diameter. For abrasive waterjets, the addition of an abrasive material conjoins onto the stream of water before leaving through the jewel.
The machinery and software also decide how quickly the jet is passed through the material. Exact speed depends on the nature of the cut and the material in use, and speed optimization can result in more efficient cuts.
The Advantages of Waterjet Drilling
Manufacturers use the water jet drill to make precise cuts when other conventional drilling tools would not be suitable. These drills work well in several circumstances:
- Compatibility: Jets can be used on materials that are sensitive to the heat generated from other cutting methods. For instance, certain plastics or metals might warp under heat stress.
- High precision: They are precise and can make specific cuts, such as sharp corners, holes, or other shapes. Specialized software and the use of various 3D nozzle shapes can ensure accurate cutting every time.
- Versatility: The water stream itself can be changed on the fly, and the software can be reprogrammed to handle a wide variety of shapes and materials. As a result, any type of cutting job can be handled this way.
- Sustainability: Because of this precision, water jets result in less scrap material, and the leftover water is still clean enough to be disposed of in a drain. Even the abrasive is non-toxic and recyclable.
- Safety: Water jet operators are not exposed to the smoke, fumes, or dust particles that otherwise would be involved in other cutting methods.
These strengths have resulted in a high demand for waterjet cutting instruments, hence why the tools are so readily available from various manufacturers globally.
Compatible Materials
The benefits of waterjets CNC cutting machines mean that manufacturers use them for a wide variety of applications, such as cutting through:
- Rubber
- Plastic
- Stone
- Glass
- Quartz
- Metal
- Textiles
- Food
This last point is particularly interesting; waterjet technology has been used to cut through meat. Since the water is drained afterward, the risk of cross-contamination is almost nonexistent.
However, there are exceptions to these use cases. Depending on surface roughness, waterjets cannot cut materials that are too hard, such as diamonds and certain ceramics. They are also not suitable for composite materials or tempered glass, which is designed to shatter intentionally under stress.
Applications of Waterjets
Waterjet machine shops serve all types of clients in need of precision cutting and drilling, such as:
- Aerospace Industry in the production of aluminum, titanium, aeronautical materials, and other exotic metals.
- Manufacturing for machine parts or assembly line goods.
- Automotive Industry for prototyping or production purposes.
- Educational institutions are even using waterjets to educate students on programming and operating procedures.
Waterjets can also be considered all-around useful tools for a variety of general-purpose applications, as their setup and operation are fairly straightforward.
Comparisons with Other Cutting Methods
Waterjets are clearly not the only option available to industrial facilities. Other methods of cutting include lasers, EDM, milling, punch presses, and plasma, and flame cutting.
Lasers
Whether gas or solid-state, a laser can be used to vaporize the material for cutting or drilling. The heat generated is not too significant, and the risk of cross-contamination is low.
However, waterjets are still more versatile and can work with a wider variety of materials and thicknesses than lasers can. With laser cutting, some material distortion could be possible, while there is no material distortion with waterjet cutting. Lasers also have a small risk of fires or vaporized fumes arising from the process. The price of a laser cutting system and its maintenance is also fairly high compared to jets.
EDM
Electrical Discharge Machining uses electrical arcs to melt and vaporize the material, while a non-conducting fluid washes away the excess. EDMs excel in creating intricate patterns.
By comparison, waterjets offer
faster operation and more versatility, as EDM only works on conducting materials like metals. The risk of heat is also a factor to consider with EDM.
Milling
Milling machines have multiple axes of cutting implements to achieve fast and precise results, even compared to some waterjets.
At the same time, the setup and cleanup of a waterjet process is still faster by comparison. You don’t have to hold the material in place like you do with milling either. Some industries even complement a milling machine with a waterjet.
Punch Presses
Using several tons of pressure, a punch press is commonly used for minting coins and stamping out parts of a metal.
However, you have to consider the cost of creating the dies and punches involved in the process. Jets can be less expensive in this regard and can work with more types of materials. Lateral force must be considered with a punch press, whereas it’s almost negligible with a waterjet.
Plasma
Plasma cutting combines an electrical arc with a high-speed stream of gas, which turns the latter into hot plasma. This process is incredibly fast, even for thick metals.
Waterjets obviously have the advantage in that the temperature involved is far lower. High heat, for instance, can melt or destroy certain laminates or other materials.
The Cost of a Waterjet Cutting System
The customers of waterjet technology can range from casual hobbyists to industrial enterprises, so it’s natural to believe that the systems range greatly in price and precision. A full waterjet system will include:
- A high-pressure pump for water capable of handling a range of pressures
- Machinery to position and move the nozzle
- Tank for catching the excess water
- Optional abrasive substance feed
- A power source with sufficient amperage
Many pumps may require up to 50 amps to run and might need a starting amperage of around 250 amps.
You can expect the price to range from several thousand to hundreds of thousands of dollars, with most prices falling in the $5,000 to $600,000 range. An industrial facility might use a $200,000 model.
Looking for a Manufacturing Partner?
GN Corporations has everything you need to go from idea to fully manufactured products.
Discover how other companies are transforming their approach to manufacturing using innovative
GN 4.0 technology.
Ready to learn more?Book a meeting today and see what it’s like to work with a technology-driven tier-1 supplier.