What Is Deep Hole Drilling and How Does It Work?
Many industrial applications involve the creation of a “deep hole” where the depth is ten times the diameter. Specialized machinery with a specific deep hole drilling tool is required to drill straight holes.
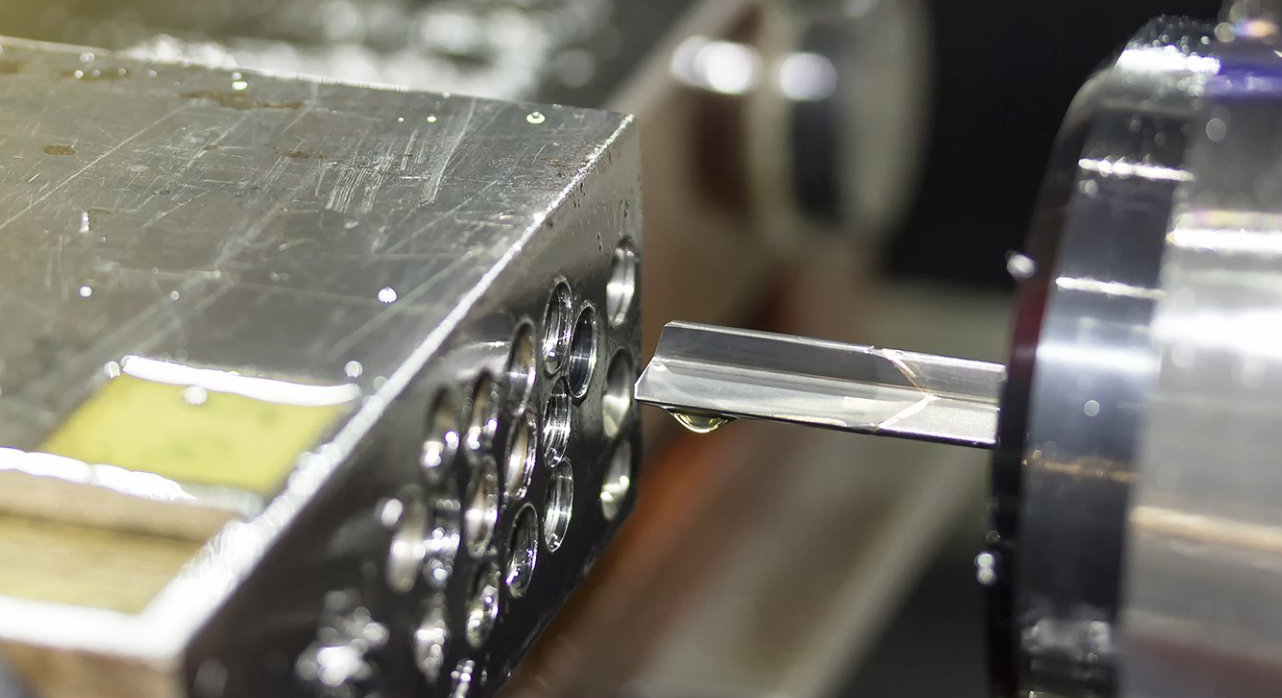
The practice began with the creation of gun barrels but later expanded into the medical tooling industry as well as the creation of plastic injection molds along with many others.
There are two primary methods for deep hole drilling: BTA drilling and gun drilling. Both use a type of coolant to help get rid of material chips during the cutting procedure, even at extreme depths. The result is a specialized cutting instrument that can complete jobs other types of drills cannot.
The Issue: Chip Removal During Deep Hole Drilling Process
Whether you’re using specialized gun drilling tools or just a regular CNC milling machine, the issue of chips and how to remove them from the drilling process is part of the challenge of deep hole drilling.
If left unattended, chips can jam the drill, harm the surface of the hole, or otherwise cause inefficiencies. Machinists carefully choose the type of tooling and coolant for better chip control and to help solve this problem.
- Pressurized coolant, especially at the tip of the tool, pushes chips out of the way properly, and coolant delivered along the length of the drill bit forces the chips up and out of the hole.
- The type of drill can also impact the ability to remove chips thanks to differences in tip geometry. A parabolic flute, for instance, works well for this purpose.
- Some machines use a “peck drilling” technique, where the drill is occasionally retracted to break up chips into smaller, more digestible bits.
The “peck” maneuver should be repeated more often the deeper into the hole you go. The further the retraction, the more chips are evacuated, but the speed of the entire process is slowed down as well. Above all, you want to make sure no chips end up at the bottom of the hole, or you risk making the drilling process more challenging.
The BTA Drilling Process
This method of deep hole drilling was first created in the 1940s by the Boring and Trepanning Association. A hollow tool enters the hole and pushes pressurized coolant onto its outside during the drilling process. Excess material is removed through the internal hole in the drill.
The Gun Drilling Process
A gun drilling machine, in contrast, uses a long, thin cutting instrument for straighter results. The drill comes in two parts: a flute cutting edge and a coolant hole separate. Just like with the BTA process, the material is removed effectively during the gun drilling process.
Depending on your precision needs, you might be able to get the job done with just a CNC gun drilling machine. Otherwise, specialized equipment is required for more accurate work.
Which One Do You Choose?
BTA drilling, by nature of its design, can achieve far higher drill feed rates than gun drilling, partly thanks to its efficient chip evacuation system. It can also work with larger diameter holes: from 20 to 200 millimeters.
Gun drilling, however, works best in smaller diameter hole sizes of up to 50 millimetres. It’s also ideal for extremely deep holes.
Designing a Deep Hole Drilling Process
The takeaway here is that your plans for deep hole drilling should depend on the nature of the work. G-Code programmers must implement a variety of factors to create a custom drilling cycle:
- Pecking can be used to clear out chips. Exactly when to start pecking and how far you want to retract the drill depends on how far along you are in the drilling procedure.
- Feed speed must vary the deeper you go as well. Reducing the spindle rotations per minute may be recommended.
- Any combination of the above strategies will be necessary. What you have to decide is exactly when each tactic is used. You might be able to achieve a faster overall cutting speed without risking chip accumulation with a custom cycle.
Whether you’re using gun drilling or BTA drilling, having these considerations in mind is important for the machinist to achieve an efficient process without risk to the equipment.
Deep hole drilling applications are used across a wide range of industries, from oil and gas, aerospace, to other heavy industries. If you are working on a deep hole drilling project and are looking for a partner who provides high precision
deep hole drilling services, then GN is the right partner for you.
Here at GN, we have the tools and expertise you need to get your next deep hole drilling job done right.
Get in touch with us today.