Aerospace CNC Machining - A Comprehensive Guide
Computer Numerical Control (CNC) technology has transformed aerospace manufacturing by allowing for unprecedented precision and durability. Advancements in several key technologies, such as robotics, automation, and machine learning, have powered the growth of CNC machining and its applications in a wide range of industries — including CNC machining aerospace.
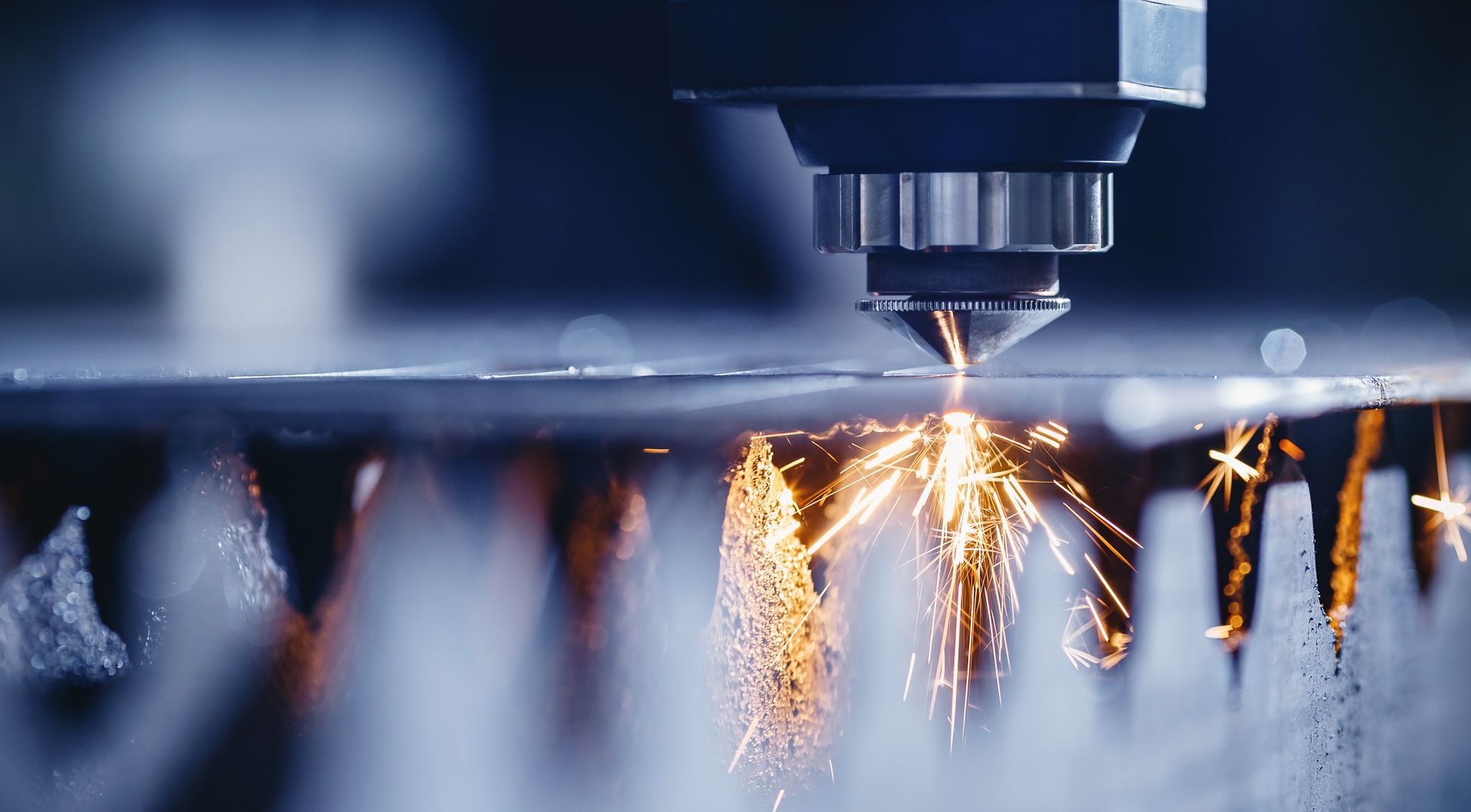
CNC machining is capable of working with a wide range of materials without sacrificing integrity. This new method has become increasingly important for manufacturing the various complex components required throughout the aerospace sector.
So, let’s explore the role of CNC aerospace parts and how it’s transforming the industry.
What Is Aerospace CNC Machining?
This new machining method allows for on-demand production and rapid prototyping and ensures the high degree of accuracy required by critical components throughout the industry. CNC aerospace machining leverages advanced manufacturing equipment and leading-edge software to reach extreme precision and durability, both crucial attributes for the aerospace industry.
Other machining methods are still used for many components in aerospace applications. Still, critical components that demand precision and work with durable materials can significantly benefit from CNC aerospace machining. So, let’s dive deeper into how CNC machining has played a vital role in the aerospace industry.
CNC Machining in Aircraft Manufacturing
Aviation and aerospace component manufacturing is a highly regulated industry, and for good reason — any defects in parts can have disastrous consequences.
The CNC machining process in aircraft component production allows for the precision machining of critical components, ensuring consistent quality. The equipment and technology used in CNC machining allow for achieving complex geometrical designs within tight tolerances, which is why it has become crucial for the aerospace industry.
CNC machining in the aerospace industry is used to manufacture vital components with strict requirements, including:
- Engine components
- Turbine blades
- Aircraft structural parts
- Frames
The equipment and technology that enable CNC manufacturing have allowed for a new level of accuracy for these critical components. Additionally, CNC machining methods can work with a wide range of materials to produce durable and high-quality parts.
The Role of CNC Machining in Aerospace Component Manufacturing
Aerospace manufacturing companies use CNC machining both for prototyping and manufacturing. CNC can be used to prototype and contribute to ongoing concept development, testing new designs, and validating the use cases of new components.
CNC machining can work with complex designs at scale and at the individual level to allow for quick iterations and refinement before proceeding to full production. Aerospace component manufacturing requires precision and reliability, making CNC a perfect option.
Once a design is complete, CNC machining can then take on rapid manufacturing. The
5-axis and 9-axis machining processes are capable of allowing for the on-demand production of aerospace parts, which shortens lead times and reduces overall production costs.
Materials Used in Aerospace CNC Machining
Aerospace CNC can work with a variety of materials, meeting the unique needs of complex parts with low tolerances. Common materials used for CNC machining aerospace parts include the following:
- Titanium alloys: Known for its exceptional strength-to-weight ratio while also offering excellent resistance to heat and corrosion. This metal is heavier than aluminum but lighter than steel, giving it widespread utility. Steel can be found in some components, but it’s generally considered too heavy for many applications, and titanium is used instead. Titanium alloys are used in planes such as the Lockheed SR-71 Blackbird.
- Aluminum: This metal is commonly used in commercial and cargo aircraft due to its lightweight and low density. Aluminum frames contribute to better fuel efficiency while also offering corrosion resistance. The Boeing 747 uses aluminum to benefit from reduced weight and high durability.
- High-performance plastics: Plastics are found throughout the interior cabin components and some structural parts. Utilizing plastics when possible helps reduce weight, provide high corrosion resistance, and provide flexibility to sensitive areas of the craft.
Aerospace encompasses cargo planes, military aircraft, and commercial transport airplanes. Different materials are favored for varying aircraft based on which attributes are necessary. The materials we explored above can all be used in aerospace CNC machined parts.
Customization in Aerospace Component Manufacturing
Aerospace machined parts need to meet complex and custom designs, making finding a machining partner challenging. Fortunately, CNC machining can create custom parts without sacrificing durability or precision.
Custom aerospace machining can be done with the right CNC partner who has the equipment and skillset to prototype and mass-produce your custom designs. It’s crucial to make sure any potential partner has the equipment and skill necessary to work with the materials you need and provide the necessary precision.
Attain High Precision and Strict Tolerances in Aerospace CNC Machining Processes
CNC machining can use 5 and 9-axis milling machines, both of which can machine complex parts and meet strict tolerances. Precision CNC for aerospace can use either machine depending on the component, both of which are improvements on traditional 3-axis machines.
Many projects can use 5-axis machines, which are capable of machining complex geometric shapes with a high degree of accuracy. These machines are also able to add surface finishes and are commonly used by precision aerospace CNC machining parts manufacturers.
A 9-axis CNC machine introduces the ability to turn and rotate the component. These machines are similar to 5-axis machines but have a turning center, providing enhanced versatility, a high degree of precision, and consistent results.
Both types of machines are used throughout precision machining aerospace due to their ability to meet tight tolerances without sacrificing durability.
Applying Finishes and Coatings to Aerospace CNC Machined Components
Aerospace components often require specialized finishes or coatings before they can be used in an aircraft. CNC machining processes can finalize the project with finishes and coatings, so you don’t need to involve another manufacturer.
Some of the finishes and coatings used in aerospace CNC components and the benefits of using them include:
- Hard coating: This type of coating calls for applying materials like titanium nitrate to improve wear resistance and reduce friction.
- Painting: Many painting tasks are for aesthetic purposes, but aerospace painting also adds weather resistance and is more durable than other types of paint.
- Thermal spray coating: Thermal sprays can be ceramics, alloys, or metals, with all of them aiming to add a protective coating to the component.
- Anodizing: This common process forms a corrosion-resistant oxide layer on aluminum parts. Anodized aluminum is widely used to enhance wear resistance and insulation.
- Powder coating: This coating is a free-flowing dry powder that is used to provide a durable finish. Powder coatings can enhance resistance to scratching, chipping, and corrosion.
With other processes, you may need to send components to other providers for finishes and coating. Fortunately, CNC machining providers can offer many types of coating you’ll need for any project.
Quality Control and Certification
Precision machining aerospace relies on robust quality control practices, while manufacturers also need to be certified to meet industry standards. An ideal quality control workflow will include the following steps:
- Material inspection: Before manufacturing begins, manufacturers should inspect raw materials to ensure they are up to standards. Even the best process will produce lackluster results if they use low-quality materials.
- Frequent calibration: CNC machines should be regularly calibrated to ensure they maintain accuracy throughout operations.
- Process validation: Every step throughout the CNC machining process must be validated to ensure design specifications are met.
- Documentation and traceability: Detailed records must be kept from material sources to the result to industry standards and certifications. Documentation also allows your teams to more easily investigate the cause of any defects.
Additionally, CNC machining organizations need the following certifications; otherwise, your compliance standing may be jeopardized:
- ISO 9001: While not aerospace-specific, ISO 9001 is a fundamental quality management certification throughout the manufacturing industry.
- AS9100: This certification is a standardized quality management system for aerospace, which expands on ISO 9001 requirements.
- FAA Certifications: Companies may require certification from the Federal Aviation Administration to ensure manufacturing requirements.
- NADCAP (National Aerospace and Defense Contractors Accreditation Program): NADCAP is a global accreditation program focusing on engineering, defense, and related industries. This accreditation focuses on quality assurance and specialized processes.
CNC Automation and Robotics in Aerospace Industry
It’s no secret that robotics and automation are prevalent within the aerospace industry, including the latest CNC machining advancements. CNC leverages advanced 5-axis and 9-axis machines powered by leading-edge machine learning algorithms to provide a new level of precision.
Now, CNC machines allow for increased productivity and efficiency. There is a significant reduction in human error and improved safety by leveraging these technologies.
Additionally, material handling and tooling can be automated during the CNC process for additional gains in productivity and accuracy. These technologies also improve robotic inspection and quality control processes. Read our blog post on The Advantages of CNC Machine Automation.
Advancements and Innovations in CNC Technology for Aerospace
CNC technology has come a long way in recent years as it benefits from advancements in several key technologies, such as robotics and machine learning. Now, it’s possible to benefit from high-speed machining and multi-axis capabilities to take on complex part production without sacrificing accuracy.
In addition, additive manufacturing and CNC hybrid technologies have provided immense benefits for the aerospace industry. Integrating 3D printing with CNC processes allows for faster lead times, higher quality, and reduced costs.
Future Outlook of Aerospace CNC Machining
There are still challenges facing
CNC machining in aerospace, along with future trends shaping its continued evolution.
Some of the main challenges facing the aerospace industry’s adoption of CNC machining include cost considerations and maintenance. Initially, buying the machines, training the right teams to use them, and ongoing maintenance can be costly. That’s why many manufacturers have chosen to work with specialists in CNC machining.
The growing demand for lightweight composite material is driving the growth of CNC machining for aerospace. CNC machining is capable of working with these advanced materials while still ensuring the accuracy of the end product.
CNC technology is capable of adapting to the new challenges posed by the latest materials to allow the industry to adapt.
CNC Machining is Driving Innovation and Efficiency in Aerospace
The significance of CNC machining in the aerospace industry is already significant, but there is still potential for further advancements and integration of the technology and equipment.
CNC machining allows for entirely new prototyping processes, quick iterations of new designs, and on-demand production. Additionally, the accuracy of the 5-axis and 9-axis, combined with being able to work with a wide variety of materials, allows it to produce critical components throughout the industry.
It’s crucial to work with a CNC machining expert who has the experience to take on your projects and reliably manufacture durable parts. Take the time to look at several aerospace machining companies to find the right partner with the skill and reputation for your needs.
Are you ready to learn why so many manufacturers in industries with strict requirements have shifted to
CNC machining?
Contact us today to learn more and receive a quote for your next project.