What Types of Industrial Protective Coatings Does GN Corp Offer?
What do industrial structures, equipment, automobiles, appliances, and tools all have in common? They all work with the protection of industrial coatings, keeping themselves safe from corrosion and regular wear and tear damage thanks to a layer of industrial paint.
For companies in the manufacturing industry to get the most longevity out of their hardware, industrial coatings of all types are available to strengthen your tools.
But how exactly do they work, what are their variations, and what advantages does each one bring? Read on to learn more about protective coatings and the services GN Corp offers.
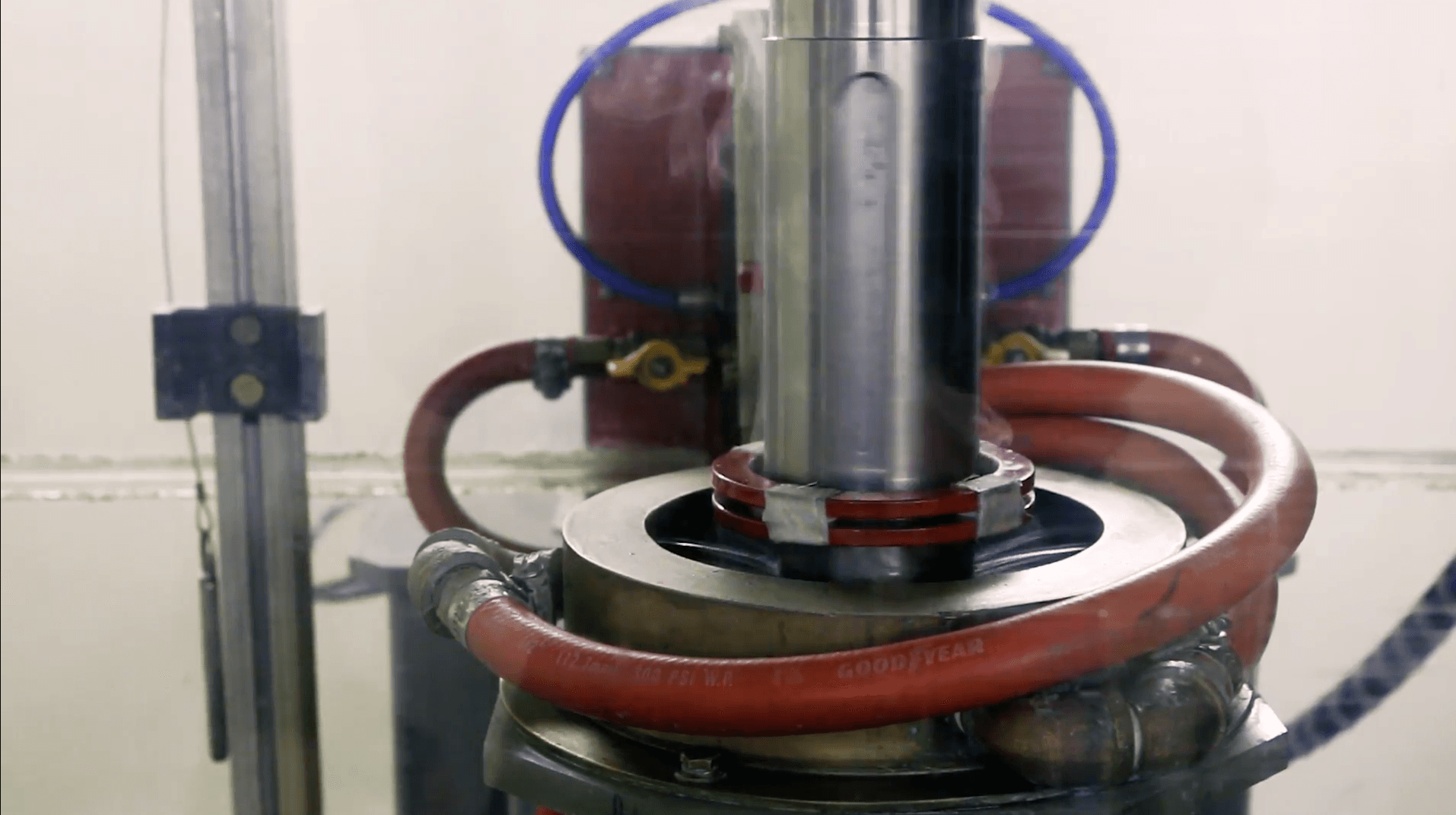
Industrial equipment must withstand the harsh conditions and use cases common in manufacturing, from corrosion to inclement weather. For example, steel tends to rust when exposed to water or oxygen, especially salt water or acid rain. And concrete tends to break down when in contact with water and the trace chemicals dissolved within it.
Factories protect their steel, concrete, and a wide variety of customizable components by coating them with specialized paints. They apply a primer first and then add the paint and some sealant for extra protection. Applications of these paints include:
- Factory floors, which face daily wear-and-tear damage from heavy machinery.
- Coil coatings within electronic components, household appliances, and car parts.
- Culinary pans like teflon that come with heat-resistant coatings.
- Food and beverage cans that must withstand the sterilization process and resist corrosion or leakages.
- Aerospace engineering Even NASA uses industrial paints for spacecraft to protect metals from extreme conditions in outer space, particularly during atmospheric re-entry.
Industrial paint also provides some aesthetic appeal and can enhance the look of certain structures whenever the project calls for it.
The Many Types of Coatings with Industrial Applications?
You’ll find these coatings across various applications, but the ones the industrial sector uses the most follow.
Zinc Phosphate Coating
A zinc phosphate coating, present on steel and iron equipment, comes in two parts. The phosphate prevents corrosion and helps paint stick to the surface more readily, while the zinc houses oils that keep rust at bay.
Applying a zinc phosphate coating involves crystallization, a chemical reaction on the metal substrate that produces a layer of insoluble zinc. The resulting applications include:
- Improving friction between two sliding components
- Allowing paint to bond to the surface better thanks to the porous nature of the coating
- Preventing rust and galling in threaded components to improve efficiency
It’s clear why zinc phosphate is a common choice for industries like mining, construction, and drilling.
Fluoropolymer Coating
By combining industrial resins with various lubricants, fluoropolymer is a dry, smooth, and slick coating that resists solvents, acids, and bases. Factories use these coatings for:
- Chemical corrosion resistance
- Preventing friction and galling damage
- Electrical resistance
- Making surfaces non-stick
You might have heard of Teflon, one of the most well-known applications of fluoropolymer coatings, but other applications include fasteners and OEM components to improve their longevity.
Polyurethane Coating
A strong line of defense against abrasion and wear and tear damage, polyurethane coatings have the added benefit of keeping a colorful, high-gloss finish on certain surfaces. They have immense potential in outdoor environments too, thanks to UV resistance and waterproofing.
Chromate Conversion Coating
You’ve likely seen screws and other tools in a greenish-yellow color. These metals have this chromate conversion coating to protect their longevity and abrasion resistance.
Also known as an alodine coating, this type of industrial paint helps:
- Inhibit corrosion
- Promote electrical conductivity
- Prime a surface for paint
Application involves immersing the metals within a chemical bath until the coating forms, though some factories choose to spray on the coating.
Epoxy Coating
Epoxy coatings come in many variations depending on the exact mixture and ratio of epoxies in the coating. The result is an incredibly versatile solution that works well in many use cases. On top of durability against abrasion, epoxies are well-known for their immense resistance to heat.
Most businesses apply epoxy as part of an overall system. For instance, a surface might start with a zinc-based initial coating followed by the epoxy and then a topcoat for best performance.
Molybdenum Disulfide Coating
Another combination of resins and lubricants generates a molybdenum disulfide coating, which applies itself to surfaces through a thermal curing process. Surfaces that must bear heavy loads exceeding 250,000 psi of pressure often use this coating.
Alkyd Coating
Alkyd surfaces have proven their worth in industrial applications and can even withstand underwater and underground conditions. They can help boats, bridges, and other steel structures resist corrosion, moisture, and high temperatures.
Enamel Coating
Porcelain enamel is a layer of engineered glass that protects metal substrates like cast iron, aluminum, copper, or stainless steel. It can come in a liquid or powder coating, and some companies use an enamel clear coat spray paint for easy application.
The advantages of this enamel are:
- Withstanding high temperatures
- Scratch and corrosion resistance
- Ability to keep its color in the long-term
On top of industrial applications, enamel coatings have uses in the home with water boilers, cooking ranges, washing machines, and architectural panels and tubes.
Discover More Applications of These and Other Industrial Paints from GN Corp
Industrial paints go beyond making structures look prettier. Those ranging from zinc phosphate to fluoropolymer, chromate conversion, molybdenum disulfide, and enamel help protect metal substrates from the harsh conditions of the factory floor. Companies use these coatings when corrosion, friction, rust, and scratches threaten the productivity of their equipment and tools.
Need industry-specific coatings to protect your industrial equipment and components? Choose a supplier with up to date industry certifications, and over 5 decades of experience in the manufacturing sector like GN Corp. GN Corp is one of the few suppliers who work cohesively with you to design sourcing strategies and take control of the cost and quality of your raw materials.
Discover how our data-driven approach helps you
finalize the perfect supply chain for your manufacturing process.