What is Industry 4.0: A Deep Dive Into the Future of Manufacturing
It shouldn’t come as a surprise that technology is rapidly changing the way manufacturers produce goods.
We’re now on the fourth iteration of the Industrial Revolution—better known as Industry 4.0—and it’s allowing manufacturing firms to reimagine their operations with a renewed focus on technology, analytics, and process efficiency.
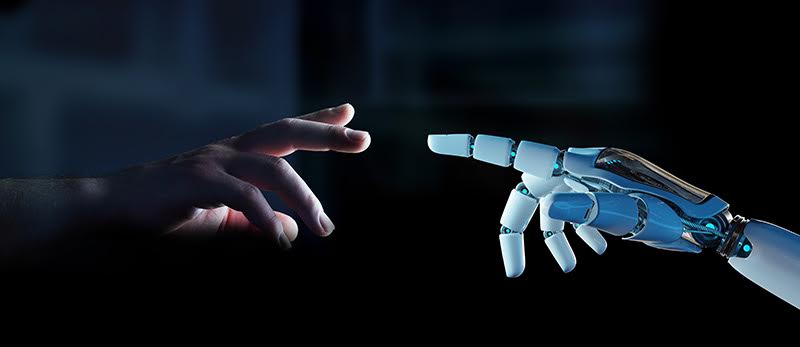
Industry 4.0 is made up of four key technologies, with new ones finding their way into the manufacturing sector as they’re developed. The big four are the Internet of Things (IoT), artificial intelligence (AI), cloud infrastructure, and big data/analytics.
Research shows that 72% of manufacturers credit IoT as the
most important Industry 4.0 technology of the four.
Industry 4.0 includes far more than these four technologies, however. Nanotechnology, advancements in robotics, improved sensors, and even blockchain technology are included in the latest industrial revolution.
The market for these technologies, collectively called the Industry 4.0 market, is anticipated to grow from
USD$64.9 billion in 2021 to a staggering USD$165.5 billion by 2026. Manufacturing is already transforming and businesses that are late to adopt these technologies will likely fall behind their competition.
So, what does Industry 4.0 entail? In this post, we’ll examine how it’s transforming the way we manufacture products globally, as well as how we got here, real-world use cases, and more.
What is Industry 4.0?
Industry 4.0 describes the rise of automated systems and enhanced data exchange technology within the manufacturing industry. It’s much deeper than just saying “automation,” however. It’s about intelligent factories where various technologies work harmoniously together to increase manufacturing efficiency, reduce errors, and reduce the need for human capital.
Here at GN Corporation, we’ve embraced Industry 4.0 through the creation of our industry-leading
GN 4.0 platform.
Manufacturers that embrace Industry 4.0 will significantly transform their operations and production processes through sophisticated sensors and analytics that provide real-time insights into their production lines. An Industry 4.0 manufacturer will have sensors armed with machine learning (ML) feeding valuable data to other machines to aid in any number of tasks, such as quality control, error detection, and process optimization.
Every technology involved in Industry 4.0 is still in active development. As each technology reaches new heights, manufacturers can enact those improvements to see immediate changes in their operations.
How Does Industry 4.0 Differ from Industry 3.0?
Industry 4.0 didn’t happen overnight, it’s been a slow and steady evolution of the technologies that signaled Industry 3.0.
- Industry 1.0: Also known as the first Industrial Revolution, was the introduction of mechanical production facilities using steam-powered machines.
- Industry 2.0: Introduced electricity and the assembly line, which dramatically increased productivity.
- Industry 3.0: It began in the final few decades of the 20th century and saw the integration of technologies, such as integrated circuits and transistors to the factory floor. These technologies increased speed, improved accuracy, and freed up the workforce from menial tasks.
As Industry 3.0 technology continued to advance, software systems were introduced that created advanced management processes, such as enterprise resource planning, shipping logistics, inventory management, and more.
So how did we get to Industry 4.0? It was powered largely by manufacturers’ investments, new advancements in ML and AI technology, and the emergence of the Internet and cloud technology. All of this led to a new way for devices and smart machines to be interconnected and share information — leading to the digital transformation of production lines.
The concept of Industry 4.0 was first introduced in the 1990s when cyber-physical systems (CPS) allowed the machines on the production floor to communicate more effectively. The line between the digital and physical worlds became blurred and catalyzed further innovation, such as real-time information sharing involving cloud computing.
Now, Industry 4.0 is still gaining momentum and directly funding further research and development of every technology involved.
Industry 4.0 Technologies
You can define Industry 4.0 technologies as any innovation that creates more flexible automation, increases the intelligence of the factory, and pushes the boundaries of connectivity. Let’s explore the big four technologies and provide a brief overview of other innovations making waves in the manufacturing business.
Industrial Internet of Things
We’ve seen many consumer-level applications of the Internet of Things emerge, but the most powerful application is the Industrial Internet of Things.
This technology refers to a network of physical devices and machines that are digitally interconnected to facilitate the exchange of data through the Internet. Industrial IoT is composed of various sensors, RFID tags, software systems, and specialized electronics all integrated to provide real-time data to a cloud-based system. Every device can pull the data it needs from the cloud, including a monitoring dashboard that provides a comprehensive view of the production floor.
Artificial Intelligence and Machine Learning
Even though there are differences between artificial intelligence (AI) and machine learning (ML), they are typically considered one of the big four technologies as a combined innovation.
AI and ML aim to take full advantage of every byte of data generated throughout the entire operation, extending beyond the production floor. Information can be gathered from across every business unit to make algorithms smarter and better equipped for their designated task, even including data provided by partners, vendors, and other third-party sources. ML is widely used in error detection to catch faulty units before they are fully produced, while AI has applications ranging from predictive maintenance to demand forecasting. For example: see
how artificial intelligence contributes to aerospace parts manufacturing
Cloud Computing
Manufacturers are no strangers to collecting and storing data to help improve production efficiency. However, other Industry 4.0 technologies have made it impractical for humans to sort through all of the data being generated at intense speeds and at massive volumes.
Cloud computing introduces the capability for all of this data to be stored and processed with remote servers, entirely avoiding the need for an on-premises infrastructure to accomplish this task. Almost every aspect of manufacturing has been transformed by cloud computing, from production operations to quality control to workflow management.
Big Data/Analytics
Every machine and sensor in the production facility is producing data, and that data is extremely valuable.
This data is stored in the cloud and then thoroughly analyzed with machine learning models to provide real-world insights into the current state of the manufacturing plant. Machine learning techniques are used to create powerful algorithms capable of processing all of the data being generated, including providing data visualization tools that allow humans to make sense of it all.
The above technologies may be considered the most impactful by manufacturers, but they aren’t the only ones making waves. A
survey of manufacturing companies illustrated that the following innovations have also made an impact on operations:
- Nanotechnology
- Advanced robotics
- Sensors
- Blockchain
- 3D printing
- Augmented reality
- Quantum computing
- Edge computing
It’s reasonable to expect that as each of the above technologies evolves, they’ll find more applications in the modern manufacturing world.
Example Solutions of Industry 4.0
We’ve touched on some of the applications of Industry 4.0 technologies, but how are they creating real-world solutions that actual companies are benefiting from? Below are a few examples of specific businesses embracing these innovations and experiencing excellent results:
Bosch Automotive Diesel Systems embraces IoT: The company’s Wuxi plant in China embraced Industrial IoT by implementing an RFID-based management system, embedding machines with sensors, and analyzing machine data in real-time. The technical director of the plant credited these technologies to creating faster reactions to equipment breakdowns, decreasing maintenance time, and being more agile to changeovers. They now have data-driven decisions based on real-time data.
- Volkswagen creates a new Automotive Cloud: Right alongside manufacturers are other industries making use of the same technologies. Volkswagen worked with Microsoft to create a new “Volkswagen Automotive Cloud” to provide enhanced features to their customers. Manufacturers in the automotive industry now must have the capability to transmit a large amount of data to the vehicle itself during the manufacturing process. Volkswagen used cloud computing in the manufacturing process to support the innovations made in the design of new vehicles.
- Fetch Robotics helps DHL manage operations: The robotics company Fetch Robotics developed specialized autonomous mobile robots (AMRs) to assist with locating, moving, and tracking inventory throughout the warehouse. Enacting these changes with robotic equipment allowed DHL to reduce order cycle time by up to 50%.
- GN Corporations launches GN 4.0: GN Corporation rapidly embraced the shift to Industry 4.0, creating its own proprietary system to transition all aspects of the manufacturing process to Industry 4.0 to better serve our customers in aerospace, defense, oil & gas, and other heavy industries.
Every manufacturer should explore how Industry 4.0 technologies can be integrated with their current operation to improve meaningful metrics, such as equipment effectiveness and production operations, that have a real impact on important business metrics.
What About Industry 5.0?
Many manufacturers are still putting Industry 4.0 technologies to use, but the manufacturing world is already looking to the next generation — Industry 5.0. This next stage involves leveraging human’s creative potential alongside the immensely powerful innovations that define Industry 4.0.
Industry 5.0 depends on highly-trained specialists working side-by-side with additional innovations that allow for more creative solutions and designs. Additive technologies and additional integration with sensors are hallmarks of Industry 5.0.
Additive Technologies
Additive manufacturing is the production term for what the wider world knows as 3D printing. It’s a series of specific manufacturing standards that make use of layer-by-layer manufacturing as opposed to traditional manufacturing that requires specialized machining to produce goods.
Some common additive manufacturing technologies are:
- Binder jetting
- Directed energy deposition
- Material extrusion
- Powder bed fusion
- Sheet lamination
- Vat polymerization
- Wire arc additive manufacturing
Making use of these technologies will require workers with specialized training to operate the machines and to use CAD software to design the 3D models.
Big Data and Sensors
The data already being generated by Industry 4.0 technologies requires special algorithms to process and analyze the information. Industry 5.0 is going to see more advanced sensors generating even more data. Big Data is going to be a hallmark of Industry 5.0 as it will require even greater advances in machine learning to properly process and analyze the data being stored in the cloud.
GN Corporations: Your Partner for Industry 4.0 Manufacturing
GN Corporations is at the forefront of Industry 4.0 and specializes in a proprietary line of solutions collectively known as GN 4.0.
This includes advanced machining capabilities with sophisticated machining, a robust supply chain network that allows data to flow seamlessly wherever it’s needed, advanced data analytics, and improved quality control processes.
Every aspect of GN 4.0 is designed to help our clients reach maximum efficiency without struggling to integrate these technologies alone.
Are you looking for a proven, tier-1 manufacturer that’s fully embraced everything Industry 4.0 has to offer? With our advanced manufacturing capabilities and connected factory, GN Corporations is well-positioned to handle the increased consumer demands for customized products for all volumes of production.
Book a meeting with us today and discover why we’re a trusted partner to some of the biggest companies in aerospace, oil & gas, and other industries.