Industry 4.0 Explained: How Data-Driven Manufacturing is Shaping the Future of Production
Manufacturing is undergoing a transformation, and Industry 4.0 is the name for the revolution. It’s the real, measurable shift toward innovative, faster, and more connected production systems.
For companies like GN, this future isn’t years away. It’s already here, delivering real results that matter.
Industry 4.0 uses digital transformation, automation, and real-time data to reshape manufacturers' operations and scale. Understanding what this shift means is the first step in staying competitive or getting ahead.
Keep reading to learn how connected tech, automation, and AI redefine production, why a clear implementation strategy matters, and what the future holds for manufacturers that embrace data-driven decisions.
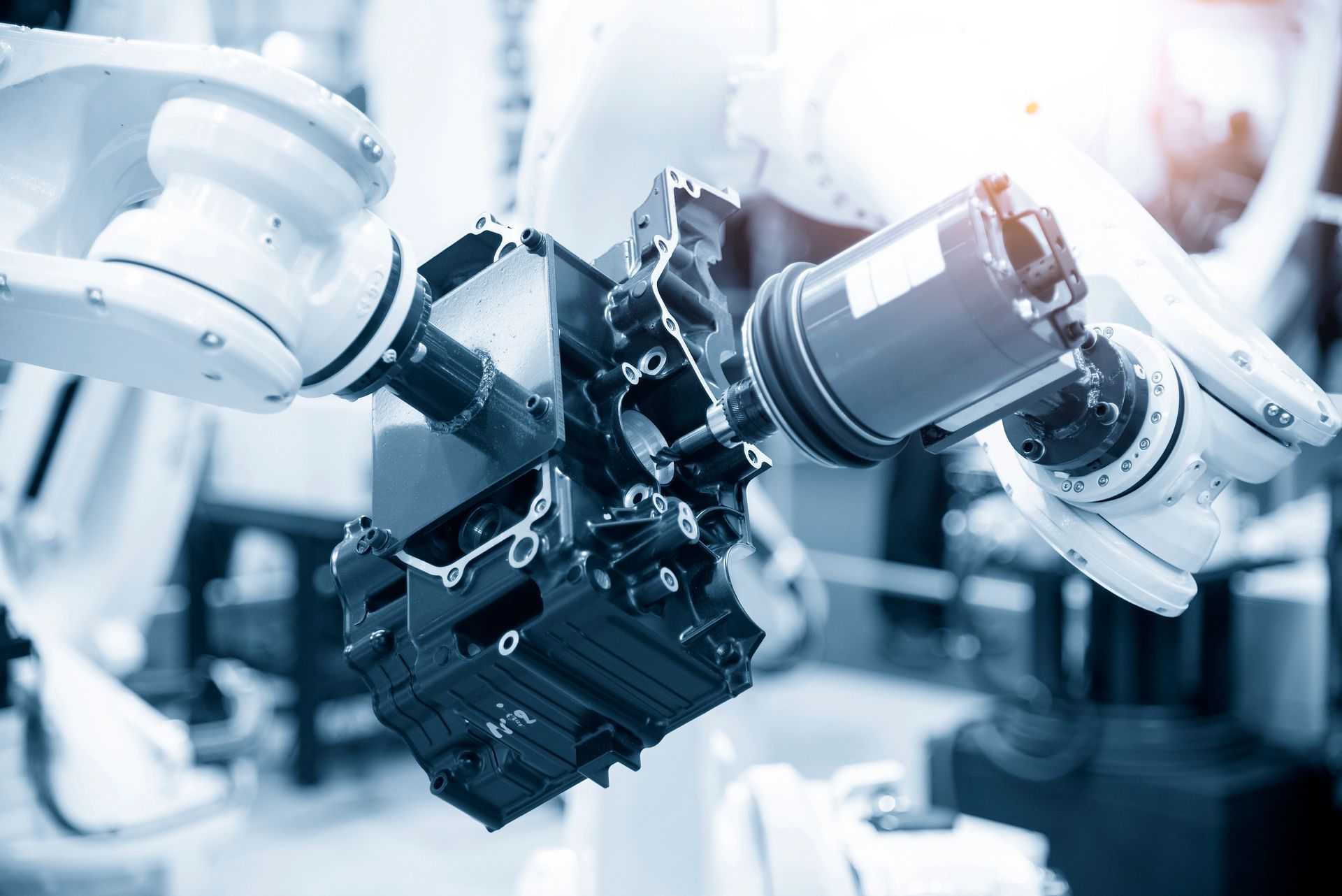
Defining Industry 4.0
Industry 4.0 refers to the fourth major shift of digital transformation in manufacturing, focused on the digital integration of physical production systems. It uses real-time data, connected devices, automation, and smart technologies to create more flexible and efficient manufacturing environments.
A Quick Look Back: From Industry 1.0 to 4.0
To see how far we’ve come, it helps to look at where we started. The evolution of modern manufacturing:
- Industry 1.0 (late 1700s–1800s): Introduced mechanical production powered by water and steam.
- Industry 2.0 (late 1800s–early 1900s): Brought mass production and electricity into factories.
- Industry 3.0 (1970s–2000s): Added computers, electronics, and basic automation.
- Industry 4.0 (2000s–present): Connects machines, people, and data to enable smart, adaptable systems.
Core Components of Industry 4.0
Modern manufacturing depends on several technologies working together. The primary building blocks are:
- IoT and IIoT: Connects machines, tools, and systems with sensors and real-time data sharing
- Big data and analytics: Collects massive data sets and turns them into insights that drive better decisions
- Artificial Intelligence: Detects patterns, makes predictions, and automates complex tasks
- Robotics: Performs repetitive or dangerous jobs with precision and consistency
- Advanced analytics: Optimizes production, improves quality, and reduces waste using real-time feedback
How Industry 4.0 Is Changing Manufacturing Worldwide
This digital shift isn’t limited to large multinationals; companies of all sizes feel the impact. Across the globe, Industry 4.0 is helping manufacturers cut costs, reduce downtime, and compete more effectively in fast-moving markets.
It’s also influencing global trade by moving supply chains closer to home through automation, IoT and
smart factories.
Key Technologies Driving Industry 4.0
The following core technologies are powering this shift and evolving quickly.
IoT and Smart Connectivity
Sensors and connected devices allow manufacturers to track equipment, monitor conditions, and make fast decisions based on live data. In GN’s facilities, for example, IoT helps identify real-time production issues and prevent unplanned downtime.
AI and Machine Learning
These tools learn from data over time, helping manufacturers predict equipment failures, spot anomalies, and fine-tune operations. AI is increasingly used in quality control systems to catch defects automatically before they cause issues.
Automation and Robotics
Today’s robotic systems go far beyond repetitive tasks. They can adapt to changes, work safely alongside people, and even make decisions based on sensor data. GN uses robotic machining and part handling to improve consistency and productivity without compromising precision.
Cloud and Edge Computing
Cloud systems store massive amounts of data and allow remote access from anywhere. Edge computing processes data where it’s generated — on the factory floor — allowing faster responses and reduced latency.
Digital Twins
A digital twin is a virtual carbon copy of a physical product, system, or process. It allows manufacturers to simulate changes, test new workflows, and identify bottlenecks without stopping production. This kind of real-time modelling helps reduce waste and optimize resources.
Implementing Advanced Manufacturing Strategies
Shifting to Industry 4.0 isn’t a plug-and-play process. It requires planning, investment, and team alignment.
Start With a Digital Assessment
Review your current processes, equipment, and data systems, identify gaps between existing capabilities and desired outcomes, then evaluate readiness for digital tools, automation, and training needs.
Build a Roadmap
Select pilot projects that offer high impact and explicit value. Define KPIs to track improvements in efficiency, quality, or uptime. Plan to scale successful pilots across other departments or facilities.
Focus on People and Culture
Adopting new tech also means changing how people work. GN emphasizes cross-training, continuous learning, and internal communication to ensure the entire team moves forward together.
Budget With ROI in Mind
Every new piece of equipment or software should deliver measurable value. Prioritize investments with substantial long-term payoffs, and track ROI in areas like downtime reduction, scrap reduction, or faster delivery cycles.
Challenges and Risks
Industry 4.0 has significant benefits, but it’s not without challenges. Knowing what to expect makes it easier to plan. Here are the common barriers to adoption:
- Cost and scalability: Digital tools can be expensive, especially when scaling multiple sites.
- Cybersecurity threats: More connectivity means higher risks of data breaches or ransomware attacks. IBM’s 2024 Cost of a Data Breach Report states that the average manufacturing breach cost was $4.88 million.
- Integration complexity: Older systems often struggle to talk to newer, more innovative platforms. A phased rollout can help avoid disruptions.
- Compliance and privacy: Regulations on data collection, storage, and usage are tightening globally, requiring more robust governance.
Success Stories and Use Cases
The best way to understand Industry 4.0 is to see it in action:
- GN’s automation success: GN has implemented intelligent automation and robotic part handling to reduce setup time and improve machining accuracy. These investments have shortened delivery timelines and made their production more scalable.
- Siemens is pioneering smart manufacturing. At its Amberg Electronics Plant in Germany, Siemens has integrated AI-powered quality control systems capable of detecting defects in real-time, significantly reducing the need for manual inspections. Additionally, the company uses Big Data Analytics to optimize its supply chain, reducing inventory costs.
- Bosch is enhancing quality and efficiency: By deploying IoT devices, Bosch monitors production processes in real-time, allowing for quick detection and correction of issues. The company also leverages Big Data Analytics to analyze production data, identifying areas for improvement.
Future Outlook of Industry 4.0
Technology is moving fast, and so is the future of manufacturing. This is what’s next on the horizon:
- 5G connectivity: Ultra-fast networks will support real-time analytics and remote control of machinery
- Smarter robots: Next-gen robots will be able to learn on the job and adapt to new tasks without reprogramming
- Sustainable manufacturing: Digital tools are helping companies use fewer resources, reduce emissions, and minimize waste
- Global supply chain shifts: Industry 4.0 is pushing more production closer to end users, thanks to flexible automation and data visibility
The Long-Term Vision
The long game of Industry 4.0 is about continuous improvement. Companies that embrace the shift, not just the tech but the mindset, are better positioned to grow, adapt, and lead.
For manufacturers like GN, it’s not about technology replacing people — it’s about giving teams the tools to solve problems faster and deliver better products every time.
Powering the Future of Manufacturing: GN’s Industry 4.0 Impact
Industry 4.0 is a smarter way to think about manufacturing. By connecting systems, using real-time data, and investing in innovation, companies can build operations that are more agile, productive, and ready for whatever comes next.
We don’t see Industry 4.0 as a future concept at GN; we’ve already embedded it into our day-to-day operations. From intelligent automation to real-time data systems, we’re helping partners improve performance, reduce waste, and stay ahead in a competitive market.
If you’re looking to modernize your manufacturing with proven, scalable solutions, we’re ready to help.